Technology drives the dynamic digital transformation, and AR advantages are not to be missed.
Industrial AR
Augmented reality, one of the most dynamically developing technologies, disrupts entertainment and light-hearted activities and suits heavy-duty applications. As we’ve already mentioned on several occasions, AR can prove itself in industrial conditions, supporting frontline workers. Immersive technologies have become a part of everyday life in manufacturing facilities, a go-to tool for thousands and thousands of technicians, engineers, and site managers carrying out their daily tasks.
Industry 4.0, also known as the Fourth Industrial Revolution, is the concept of technological changes in industries, patterns, and processes taking place due to the rapid development of new digital solutions. Augmented reality is at the forefront of ongoing changes, along with artificial intelligence and the Industrial Internet of Things. At the junction of bleeding-edge technologies and industrial transformation, significant changes happen before our eyes.
How can AR improve factory productivity?
Augmented reality is a software tool that can be used in manufacturing industries, where real-time efforts are essential for the decision-making process. From info visualization, and convenient communication, to data management, and reporting, AR proves to be an overall useful tool that changes the manufacturing industry as we know it.
While we’re discussing the general idea and not particular numbers, AR’s impact can be expressed in Overall Equipment Effectiveness (OEE). OEE is an industrial Key Performance Indicator (KPI) used to describe the overall productivity of a machine, comparing its performance to relative capacity. Implementation of various measures and efforts contributes to optimal results and, in the long run, maximizes efficiency with augmented reality in manufacturing.
What does factory productivity depend on?
Workforce
Without proper onboarding, training, and ongoing well-managed knowledge transfer, there is no chance for consistent, high productivity. A well-trained workforce and high retention facilitate efficiency, quality, and timelines while reducing downtime and eliminating errors.
Equipment and technology
The hardware side of manufacturing impacts productivity during the whole process. The better maintenance, service, and repairs, the longer the life of the equipment and machinery, and the fewer obstructions to the outcomes.
Process optimization
In manufacturing, old-school ways are one of the operational alternatives, yet, it’s worth remembering, they’re not the only possible way to go. Remaining bound to the old methods and approaches is the best way to lose market position and competitive advantage. In addition, the ever-changing world of technology requires keeping up with its pace and optimizing processes to e.g., reduce waste, eliminate inefficiencies, and streamline operations.
Supply chain management
Without supplies, the manufacturing industry would be idling on neutral. Industrial enterprises need sustainable supply chain management from raw material delivery to packaging and everything between the ore and the final product. Improving this aspect enables the timely delivery of materials and components and, in the long run, allows for bypassing disruptions in the logistics process.
Workplace safety
Productivity peaks in a working environment of high safety standards, respecting occupational health and safety regulations, and skillful execution of operations. With fewer accidents and threats to employees’ well-being, companies can achieve their objectives more efficiently and consistently instead of treating injuries, battling downtime, and responding to lawsuits.
Manufacturing efficiency doesn’t stem from a single factor or particular areas. Productivity is a total of the above-listed matters, and as such, it needs to be addressed in a comprehensive and holistic manner. Tech solutions became a reliable partner for industrial companies, enabling ongoing monitoring, evaluation, and continuous improvement to achieve set goals over time and maximize efficiency.
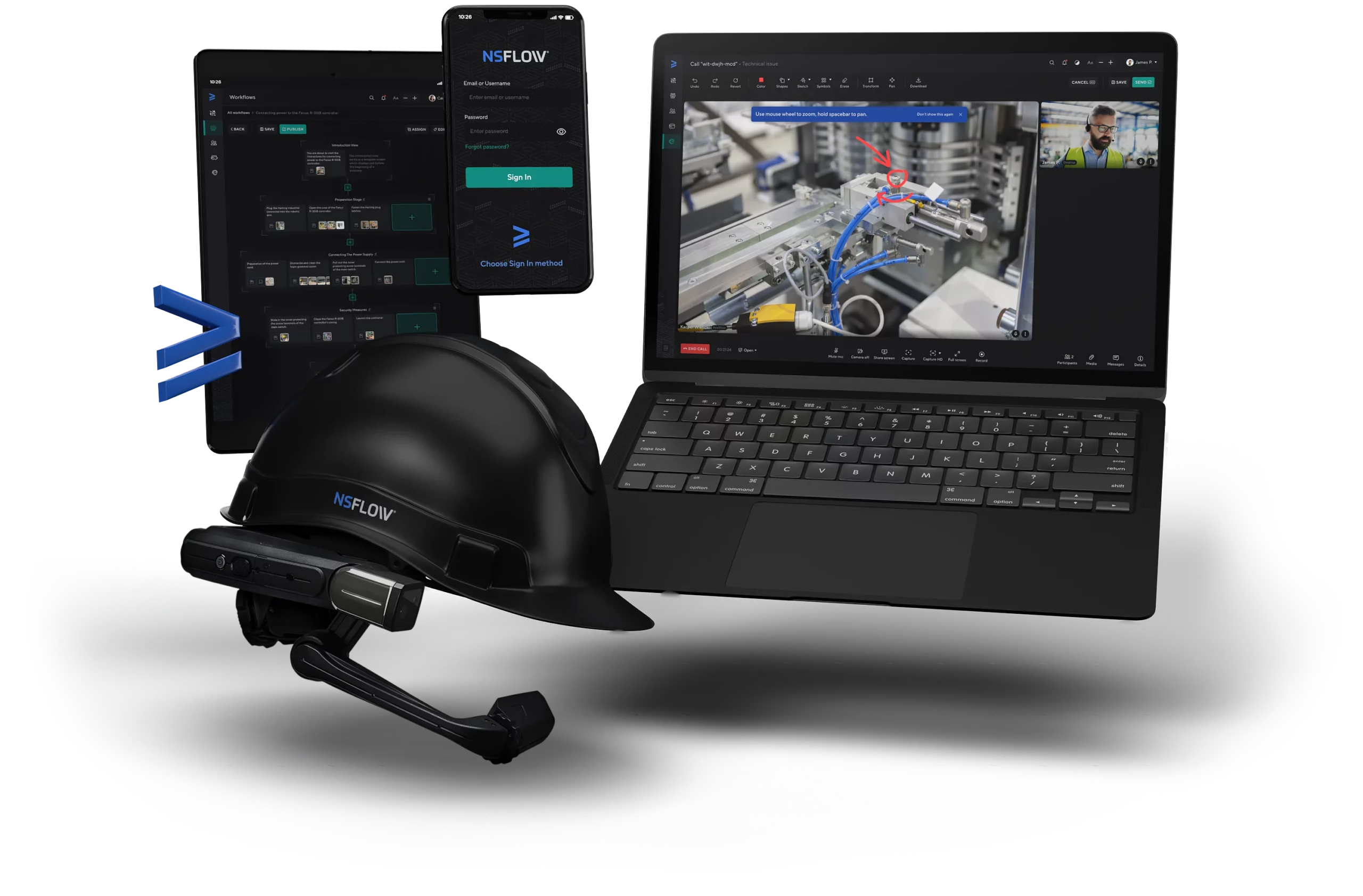
presentation to try
Nsflow in action
AR for Industry 4.0 automation
The potential of augmented reality adoption in industrial applications relies on its practical advantages. AR-powered solutions enable real-time, context-aware information delivered to individual workers, allowing them to perform faultlessly and more efficiently. Combining real-life environments with digital additions is the future-proof approach to enhanced learning, seeing, and achieving.
Examples of AR Industry 4.0 automation
While augmented reality is still a relatively new technology, its business applications are already gaining popularity. Some of the practical AR implementations include
Quality assurance
Guiding on-site personnel through complex inspection tasks, providing feedback in real-time, and highlighting areas requiring attention, it all helps reduce unplanned downtimes and improve OEE. the fewer malfunctions and breakdowns, the better the results. From the company’s point of view, decreasing the number of errors is one of the key factors to maintaining operational efficiency and competitive advantages.
Efficient training
The traditional training model entails gathering course participants in a classroom with an instructor, which requires availability at set times and places, and the usage of paper-based materials. AR-based training skips all the trouble spots – no need to rent a classroom each instructor can guide not 10 or 30 participants during a single meeting, but as many as it’s required – even the whole company at once. Additionally, digital content is easy to update and distribute and doesn’t require physical copies with their costs, weight, and nuisance in distributing and amending.
Enhanced safety
Safety matters are a sum of various efforts. A workplace, especially in industrial conditions, can’t be safe without significant attention to proper training on occupational health and safety, along with proper equipment maintenance. Augmented reality helps execute tasks in demanding conditions, and what’s more, AR training fosters the development of muscle memory. Employees performing hands-on training learn to perform actions in real-life situations with technology supporting accurate task execution.
Maintenance processes
Overseeing machinery operations requires attention to detail and monitoring tools utilization. Industrial companies introduce various approaches to maintenance (predictive and preventive types) to ensure the most beneficial assets’ status, health, and performance. Employing augmented reality for industry maintenance allows for flawless operations and swift responses to occurring abnormalities before they can disrupt the production process.
Inventory management
Augmented reality sees more than humans can perceive. Industrial AR solutions can help assess resources from the bird’s eye-view. For example, warehouse workers equipped with AR glasses can check stock information and easily identify the most efficient routes for retrieving wares from their storage locations. Supporting personnel with digital additives and hardware pieces, such as sensors and beacons, improves inventory management, at the same time reducing the error rate from the human factor.
Augmented reality in industry 4.0
Augmented reality has the potential to improve factory productivity by equipping staff with spot-on guidance, real-time information, and feedback, enabling error reduction and overall performance boost. Furthermore, with the growing adoption of technology, industrial companies are expected to experience AR-powered digital transformation and its advantages.
Curious how augmented reality can change your operations for the better? Read more about what AR can do for you and how augmented reality for manufacturing process automation can improve your results. We’re always happy to talk if you’d like to learn more about AR and Nsflow. So let us know and see for yourself.